Undergraduate Civil Engineering Seniors Literature Review on Orifice Meter Applications- Juniper Publishers
Civil Engineering Research Journal-Juniper Publishers
Abstract
In this literature review paper, undergraduate senior Civil Engineering students from California State University, Northridge, under the supervision of Dr. Tadeh Zirakian and Dr. David Boyajian, introduce a research on orifice meter and its applications in real life while analyzing the effect of variables, such as flow, velocity, pressure, and volume. Orifice flow meter is the most commonly used device for gas flow measurement. For a most accurate measurement, the orifice meter should be applied to gas flows, which are steady or vary slowly with time, are in the turbulent flow region, and are well below sonic velocity. The gas should be single phase and not contain suspended particles. Availability of sufficient permanent pressure loss is a requirement for any head-measuring device and must be considered in its application. Completion of this virtual research achieved several educational endeavors, namely enabling the students to apply their acquired engineering skills to real life scenarios and promoting the practice of communication and sharing of ideas in a diverse team setting. It is hoped that this research will help future research studies and inspire the use of orifice in hydraulic applications.
Keywords:Orifice; Hydraulic; Applications; Engineering Education; Diversity
Introduction
An Orifice Meter is a conduit and a restriction to create a pressure drop. A nozzle, venturi or thin sharp-edged orifice can be used for flow restriction. In order to use any of these devices for measurement it is necessary to empirically calibrate them. That is, to pass a known volume through the meter and note the reading in order to provide a standard for measuring other quantities. Due to the ease of duplicating and the simple construction, the thin sharp-edged orifice has been adopted as a standard and extensive calibration work has been done and is widely accepted as a standard means of measuring fluids. Provided the standard mechanics of construction are followed no further calibration is required. “The basic functionality is that as the fluid approaches the orifice the pressure increases slightly and then drops suddenly as the orifice is passed. It continues to drop until the vena contract, the point in a fluid stream where the diameter of the stream is the least, and fluid velocity is at its maximum is reached and then gradually increases until at approximately 5 to 8 diameters downstream a maximum pressure point is reached that is lower than the pressure upstream of the orifice” [1]. The decrease in pressure as the fluid passes through the orifice is a result of the increased velocity of the gas passing through the reduced area of the orifice. When the velocity decreases as the fluid leaves the orifice, the pressure increases and tends to return to its original level. All of the pressure loss is not recovered because of friction and turbulence losses in the stream. The pressure drop across the orifice increases when the rate of flow increases. When there is no flow there is no differential [2]. The differential pressure is proportional to the square of the velocity. It therefore follows that if all other factors remain constant, then the differential is proportional to the square of the rate of flow. Figure 1 illustrates a visualization of flow in an orifice plate as through water comes through the pipe and goes through the pressure instrument.
Prior Investigations
According to the research done by the S.T.B.S. College of Diploma Engineering, titled “Comparative Analysis of Different Orifice and Geometries for Pressure Drop”, measuring the pressure difference created from the reduction of the cross-sectional area of flow passage can be calculated for the flowrate. It is essential to minimize this loss to lower the energy cost necessary for flow metering. Studies show that the pressure drop across fractal-shaped orifices is lower than that of regular circular orifices of the same flow areas. In addition, shapes of perforations do not affect differential pressure, but pressure recovery has been observed with rectangular perforations. Multi-hole orifice plates have better flow features than the single hole ones. It has also been shown that when comparing the geometry of orifice plates using identical contraction ratio and thickness, sharp-edged orifice plates showed the highest dissipation capacity. Orifice plates are categorized based on stream surface profiles and geometry. Some types of orifice plates include square-edged, square-edged with 45 degrees, back-cut, sharp-edged, streamlined-approach, sloping-approach, and quadrant-edged. Through analyzing different geometries of orifice plates for pressure drop under equal diameter ratio and thickness using CFD (Computational Fluid Dynamics) analysis, results showed that the square-edged orifice plate with 45° back-cut had maximum pressure whereas minimum pressure drop was observed for the streamlinedapproach orifice plate [3].
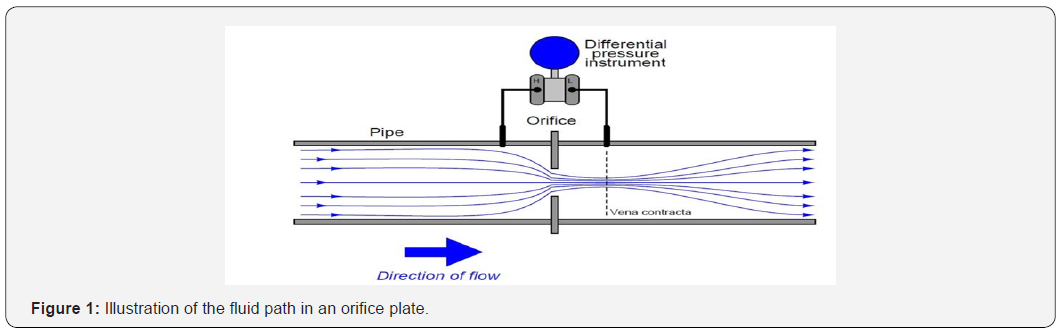
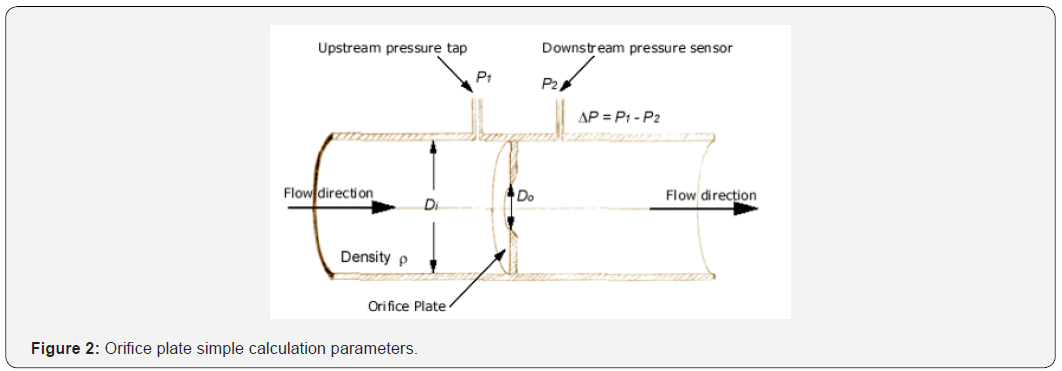
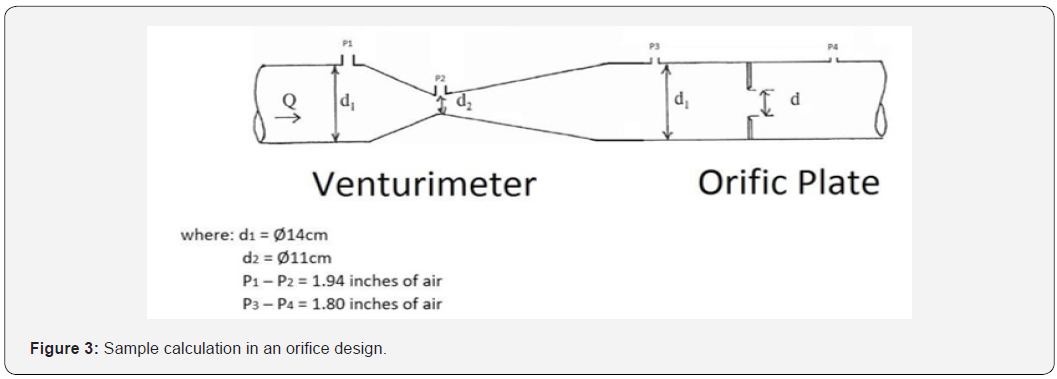
According to the research done by Emerson Automation Solution Company, “Flow can be accurately determined without the need for actual fluid flow calibration. Well established procedures convert the differential pressure into a flow rate using empirically derived coefficients. These coefficients are based on the ability to accurately measure orifice plate dimensions and pipe diameters as defined in standards combined with easily measurable characteristics of the fluid rather than on fluid flow calibrations. With the exception of the orifice meter, almost all flow meters require fluid flow calibration at flow and temperature conditions closely approximating those when the meter will be in service in order to establish accuracy. Orifice meters do not require direct fluid flow calibration and offer the advantages of being simple to operate, rugged, widely accepted, reliable and relatively inexpensive with no moving parts.” These are the major advantages of an orifice meter.
The research paper by Akshay R. Kadama, Mangesh B. Chaudharib about Acoustic Study and Behavior of Flow through orifices explains that orifices are designed either to decrease the pressure or to increase the velocity of fluid flow. When pressurized turbulent flow or normal fluid flows through an orifice, it creates sound waves, disturbances, pressure fluctuations leading to vibrations, generation of noise and cavitation at orifices. Therefore, there is a need to study the acoustics behind such flows, and to analyze the frequency spectrum, the power spectra, and the acoustics wave transmission for flow through an orifice. Different types of flows are analyzed through different shapes of orifices by depicting sound power spectra, frequency spectra etc. Some experimental results have presented for onephase and two-phase high pressurized flow through single-hole and multi-hole thick orifices. Most of the case studies have been over acoustic wave behavior in flow through sharp edged orifices placed in circular, square, and rectangular ducts. The research was carried out on the acoustic source created by turbulent flow through orifices and large eddy simulation of acoustical flow through an orifice [4]. The entrainment of cavitation and sound waves into the fluid flow through an orifice is also presented. Flow acoustic study can be applied to various industries and fields where acoustic study counts to overcome problems, to determine the effects of sound waves on orifices, to determine the behavior of flow through different shapes of orifice and to analyze the effects of entrainment of sound waves into the fluid flow on power and frequency spectrum. The acoustic study of turbulent flow at various wind speeds with low noise over orifices is explained [5].
The article titled “Determination of the uncertainty of mass flow measurement using the orifice for different values of the Reynolds number” presents the problem of estimation of uncertainty of a liquid mass flow measurement using the centric orifice plate for different values of the Reynolds number: a ratio of inertial forces to viscous forces within a fluid which is subjected to relative internal movement due to different fluid velocities [6]. The authors carried out the estimation of the uncertainty of the extended flow measurement - using the Monte Carlo numerical method, and then conducted a series of experiments on the laboratory stand for the same input data. In the studied range of Reynolds numbers 8,000
The journal titled “Investigation of variable orifice plate design for centrifugal compressor low-end performance improvement” presents a compressor with variable inlet configuration upstream of the compressor wheel, which was investigated to improve the compressor low-end performance. As a concept study, the variable inlet configuration was assumed to be a variable orifice plate which can reduce the compressor inlet flow area when it is activated. The compressor performance with and without the initial orifice plate was assessed quantitatively using both numerical and experimental methods. The results indicated that the initial orifice plate design can improve the compressor efficiency at low speed and flow rate condition. Different orifice plate designs with different setting angles to the compressor inlet main flow direction and different radial heights were also numerically studied. It was found that: (1) changing the orifice plate setting angle from 90o for the initial design to 67o can improve compressor efficiency about 0.56% at low flow rate condition; (2) increasing the orifice plate radial height from 16% of the compressor inlet radius for the initial design to 27% can improve the compressor efficiency by 1.78% at near surge condition and extend surge margin by 9% The results indicated that the radial height has larger effects on compressor performance than the setting angle at near surge flow rate. While increasing the orifice plate height variation can further improve compressor low-end efficiency and surge margin, there is an increased complexity of the actuation and control system [8].
Significance of Prior Researches
“In order to accurately measure the volume of fluid that passes through a pipe or an open channel, first the definite flow rate has to be determined. The best flow measuring device that can be used for this purpose is the Orifice Meter. The two applications of this device are to measure the flow rate of fluids in their single state, and also to measure the flow rate in a mixed state such as natural gas with water or wet stream. The industries that utilize the orifice meter are refineries, water treatment plants, natural gas industries and petrochemical plants” [9]. The most important advantages that need to be mentioned are that this measuring device is inexpensive, it’s easy to use, it occupies very little space, it can be installed in vertical or horizontal positions, and it can be used to determine flow rate in large pipes.
Supporting evidence is shown in an article from “The Journal of Fluid Engineering” where the authors underwent various tests that included sharped-edged and borda mouthpiece orifices. For more clarification, a sharped-edged orifice refers to the existing walls being sharp edged as where a borda mouthpiece orifice refers to an internal or re-entrant orifice that extends into the fluid. “The purpose of these tests was to discover how the different shaped orifices would affect the velocity flow of the fluid traveling within the pipe. In this particular case, these orifices would determine how quickly an ink-jet printer free jet would spray. It was confirmed that the shape of an orifice does in fact make a difference in the velocity of a fluid passing through that section [1]. A sharp-edged orifice compared to a borda mouthpiece would have a higher exciting velocity respectively” [3]. It is specifically based on how the fluid reacts when upon entering the orifice section of its flow. This helps to reveal that even the smallest applications of orifices are important to achieve a perfection quality of service. In Figures 2 and 3, we can see the basics of designing an orifice plate.
Educational Objectives
One of the goals of this research was to help undergraduate students develop a deeper understanding in the area of hydraulics. By conducting hands-on experiments, scholars are able to develop a better understanding of the fundamental concepts in hydrology [5]. Rather than working on individual projects separately, the research team combined their skills to work for a single cause of finding research that will benefit the industry. This project allowed every individual to use his or her strengths in order to complete the project.
As the infrastructures in America have been considered to be subpar, it is up to researchers to discover different methods to improve the infrastructure of the society. With a self-motivated group of individuals, this group of researchers has been able to deliver research that benefits the civil engineering industry as a whole. This project proves that a diverse group of individuals with different backgrounds are able to achieve their goals of completing a research project [10-12].
Conclusion
The goal of this literature review by undergraduate senior students, which summarizes some significant studies on orifice applications, was to help undergraduate students develop a deeper understanding in the area of hydraulics. Our research focused on orifice meters and their applications in real life while analyzing the impact of variables, such as flow, velocity, pressure, and volume on the functionality of orifice meters. Orifice flow meter is the most commonly used device for gas flow measurement. For a most accurate measurement, the orifice meter should be applied to gas flows, which are steady or vary slowly with time, are in the turbulent flow region, and are well below sonic velocity. The basic functionality is that as the fluid approaches the orifice the pressure increases slightly and then drops suddenly as the orifice is passed. It continues to drop until the point in a fluid stream where the diameter of the stream is the least, and fluid velocity is at its maximum is reached and then gradually increases until at approximately 5 to 8 diameters downstream a maximum pressure point is reached that is lower than the pressure upstream of the orifice. To conclude, this research study has allowed us scholars to work in an environment with a diverse group of individuals towards a greater objective. As the infrastructures in America have been considered to be subpar, it is up to researchers to discover different methods to improve the infrastructure of the society. With a self-motivated group of individuals, the group of researchers has been able to deliver research that benefits the civil engineering industry as a whole.
For more about Juniper Publishers please click on: https://juniperpublishers.com/journals.php
For more Civil Engineering articles, please click on: Civil Engineering Research Journal
https://juniperpublishers.com/cerj/CERJ.MS.ID.555780.php
Comments
Post a Comment