Organizational Effectiveness: Collaboration in an Integrated Project Team-Juniper Publishers
Juniper Publishers- Journal of Civil Engineering
Abstract
Projects in the process industry are getting more
complex from a technical as well as an organizational point of view.
These projects can be considered as series of multi-phase and
multi-discipline design and engineering activities involving
contributions from many parties on many locations. In order to
successfully perform such projects collaboration is required. This paper
presents the results of studying a refinery revamp project. In this
project the opportunity was offered to investigate the collaboration in
the project team. Objective was to study the effectiveness of the
organization in a multi-actor, multi-office and multi-discipline
environment and identify potential areas for improving the
collaboration. The method chosen was to study the business process model
and combine this with a social network analysis (SNA) via observations,
surveys and interviews. The differences shown in the comparison between
the SNA and the business process model indicated areas where the
collaboration could be improved. Furthermore, early identification of
potential overload of people has been discovered from the social network
analysis. SNA showed to be a powerful analysis method for investigating
softer factors in projects, which is not yet common practice in the
process industry.
Keywords:
Social network analysis; Multi-actor; Multi-office; Dispersed execution;
Contractor-client interaction; FEED phase; Collaboration; Business
process modeling
Abbreviations:
Social Network Analysis; FEED: Front-End Engineering and Design; PFD:
Process Flow Diagram; P&ID: Process and Utility Instrumentation
Diagrams; WBS: Work Breakdown Structure; PAM: Project Activity Model;
PRC: Project Requirement Checklist; WBS: Work Breakdown Structure; SBET:
Site Based Engineering Team
Introduction
Over the years projects in the process and energy
industry are getting bigger and more complex. But unfortunately the
performance of these projects is lagging behind. Various publications
highlight this disappointing performance of large and megaprojects in
the industry [1] and more specifically in the Oil & Gas industry [2].
This is not a trend from the last couple of years, but already a
long-standing issue in the field of project management. As early as
1987, Morris and Hough analyzed 3500 projects from all over the world
executed in the period from 1959 till 1984 [3].
They came to the staggering conclusion that these projects showed
typical overruns in expenditure and schedule between 40 and 200% (and
bigger overruns have been seen). Today, almost 30 years later, the
situation has not really improved.
The potential solutions that most practitioners and
researchers are proposing are: more attention to early involvement of
all parties concerned [4],
a seamless collaboration between owner and contractor (a real
integrated team), giving attention to the development of real
collaborative relationships and spending sufficient time on the
front-end development of the project [5].
Knowing these areas for improvement is one thing,
acting on it, as recent history shows, is still considered a challenge.
For a project that was recently initiated for the revamp of a refinery
in Western Europe of one of the large multinational oil companies (=
owner), a single engineering contractor (= contractor) has been selected
to perform the front-end engineering and design (FEED) phase and the
management of the construction phase (EPCm). The managements of both
parties have decided to deliver both phases as integrated as possible
with a single team consisting of both owner and contractor
representatives. Doing this, the intent was to form a high performing
team by giving focused attention to the way the team is organized:
improving the organizational effectiveness of the combined team. This
refinery project is facing a tight schedule with design works carried
out in parallel i.e. overlap in definition and execution phases. A
separate challenge comes from the complexity of the project team
formation. It has the work distributed over the Amsterdam and the New
Delhi offices of the contractor and the owner team is spread over the US
headquarters, the contractor's office in Amsterdam and the refinery
site office. In order to take on these challenges and to meet the
demanding project schedule, this supportive research was proposed.
This research is part of a longitudinal study into
the organizational effectiveness of a project team consisting of owner
and contractor. During the course of the project, in all phases of its
lifecycle, a number of master students will be embedded in the project
team to study the collaboration within the team and between the various
locations. In each phase and each year a different master student will
participate. This article is the first report out of the research
performed by the students over the years.
The aim of the research is to improve collaboration
among different disciplines, different actors as well as different
offices. It is an empirical study in which the project team is followed
and observed initially during the FEED phase.
The workflow methodology will be used for all three
levels of collaboration (amongst different disciplines, amongst
different actors and amongst different offices). First a business
process model will be derived for the present phase of the project.
However, the network relationship information, which is extracted from
the workflow, only tells what is the expected relationship according to
the work procedure. It basically only tells how the organization is
supposed to work (=SOLL). The real network relations in an organization
may differ and may contain more informal, untracked links, which cannot
be observed from workflow and the formal organization chart (=IST).
Therefore, Social Network Analysis is invoked to provide a view of the
real network within the project team.
Comparing the outcomes of the workflow methodology
and the Social Network Analysis can give more insights for and about the
team and answer the question how the collaboration and consequently the
organizational effectiveness can be (further) improved. The research
question that will be answered is therefore "Can a comparison of the
theoretical workflow with the real network relations identify
shortcomings in the effectiveness of the organization?" The objective of
the integrated project team, consisting of owner and main contractor,
was to find ways to enhance the collaboration between both parties and
in this way to develop and further improve the effectiveness of the
project organization.
Literature Review
Workflow methodology and business process management
The Workflow Handbook [6]
defines workflow as: "The automation of a business process, in whole or
part, during which documents, information or tasks are passed from one
participant to another for action, according to a set of procedural
rules." From a higher-level perspective, workflow can be regarded as a
representation of real work, in other words serving as a virtual
representation of actual work [7].
In recent research, many people consider Business Process Management
(BPM) to be the extension of the workflow theory of the 1990's, which
brings process awareness to the strategic and operational level [8].
Business process management consists of an explicit description and
representation of the coordination, optimization, and automation of the
enterprise assets and tasks-whether internal or external - that make up
an enterprise's business processes[9].
A business process is usually specific to a particular project, but it may follow a standard pattern used by the company[10].Within
the engineering disciplines for this particular downstream oil project
in this phase, this corresponds to the tracking of tasks and sub-tasks
according to the Work Breakdown Structure in order to deliver the final
design or product. The flow being described may refer to a document,
service or product that is being transferred from one step to the next.
Design processes in chemical and process engineering
are hard to support. This is especially true for the conceptual design
and basic engineering, in which the fundamental decisions concerning the
plant design are taken. The design process is highly creative, many
design alternatives are explored, and both unexpected and planned
feedback occurs frequently[11]. Previous research [12]
pointed out a way of improving collaboration in the chemical and
process industry by examining the workflow dependency and improving the
associated information exchange process. Schneider and Marquardt [13]
(regarded workflow as one of the three perspectives (next to software
and product data) in the design life cycle concept for the chemical
engineering projects and provided systematic information support for
interdisciplinary collaboration.
Sidhu and Volberda [14]
conducted research on a globally distributed team using the same
workflow concept. They found that due to the nature of tasks and the
associated differences in employee competencies, home offices and
distributed offices perform different value-chain activities. Similarly,
Joshi and his team adopted workflow and network methodology to
prioritize the main conflicts and problems in multinational companies[15].
Among many workflow and BPM research papers, there
are few related to process industry. In the white paper of Best
Practices in Front-End Design [16],
a rough FEED workflow is formulated which shows the main line of
activities for developing a plant design. Even though this figure is
mapped in a very high level manner, it still shows that by using
deliverables (documents) like Process Flow Diagram (PFD), Process and
Utility Instrumentation Diagrams (P&IDs), Datasheets, Plant Layout,
Capital Expenditure estimates, the design and decision making process
can be shown with a simple time sequence.
When checking the latest business process methodology [17,18],
it shows a trend to start focusing on "people" and consequently the
workflow system is re-positioned as a tool for organizational
performance studies. Strong belief is that there is a link between the
workflow-performers and the social network relationships, which reflect
the collaborative team behavior and has high impact on business success.
Battsetseg et al. [17]
summarized that most of the workflow models employ several essential
entity-types (modeling components): activity, role, performer,
application amongst others. The activities always have corresponding
roles and performers. Therefore, the dependency and links among the
tasks in the workflow actually bring together the performers in a
network relation with links representing the dependencies. Song et al. [18]
found out that "the workflow management systems are 'people systems'
that must be designed, deployed, and understood within their social and
organizational contexts."
Lewis et al. [19]
analyzed the interests and goals of different stakeholders (actors)
since these provide the specifications and requirements for the
activities. In the adaptive workflow theory, the stakeholder is an
important factor making the workflow more dynamic. Therefore, this
research will also start from the workflow point of view and broaden
this methodology to study the collaboration among project disciplines,
globally distributed offices and involved actors as a whole.
Social network analysis
Social Network Analysis (SNA) is a powerful tool from an organizational perspective [20].
It has drawn a variety of scholarly pursuits throughout the years and
its implementation developed over time. SNA has been applied in various
research domains such as collaboration, partnership, knowledge sharing
and innovation, corporate acquisitions, social media, political parties,
criminal psychology, healthy habits, disease spread [2126].
Social network analysis aims to describe the relationships between
people as complete as possible. It includes relationships maintained in
digital computer mediated interactions, or the communication, activity
for resource allocation, problem solving that is needed for work. A
so-called Sociogram in which vertices represent individuals visualizes
the results of SNA. It is a good way to discover the informal structure
within an organization, which coexists with the formal structure usually
stated in the organization chart. Besides, SNA can be used to study the
cooperative relationships across organizational boundaries:
outsourcing, joint ventures, alliances, globally distributed teams [27].
Social network information can be gathered via electronic platforms
such as email, forums and social media. However, most often the
information is gathered manually. Manual collection includes observation
and recording of activities, questionnaires or surveys, holding
interviews and reviewing diaries.
Social network analysis has its limitations. One
major drawback is that the result is difficult to judge or to interpret.
Especially because SNA is very unique, every network being studied is
different in team size, composition, location, and type of relation. It
is very difficult to have a generalized benchmark that tells what a
social network should look like. Therefore, the workflow methodology is
adopted here as a supplemental method which provides some work-related
insights and can be used to interpret the result of the social network
analysis.
Research Methodology
This research will investigate the abstract term
collaboration by attaching it to the visible workflow chain and using
the organization chart as resource to link the people with their
functions and positions. Starting from the main FEED deliverables, this
research will check how the deliverables are divided into manageable
tasks (the Work Breakdown Structure or WBS) and how these deliverables
are produced, issued and reviewed by involving the different actors
(this is what is called the workflow). In phase 1 the Practices,
Guidelines, Manuals, Checklists, Templates, Project Debriefs from both
the owner and the contractor will be studied. Based on the findings, the
network relations in the taskforce will be modelled. Every workflow is
restrained between clear start and end points. This is usually dependent
on the scope of work. During this research, the project tracked is
carrying out the Front End Engineering Design (FEED) of a refinery
revamp project. The scope of work for this FEED package will be the
scope of the workflow model. Besides this scope, the flow model is
composed of many elements. There are various types of workflow models
that have been proposed in the workflow literature and almost all employ
five essential entity-types [28]:
· Activities in a design process and their interdependencies;
· Information produced during the activities or needed for their execution;
· Roles or organizational units of the actors;
· Resources needed to complete the tasks;
· Tools required for performing the activities.
Other factors like time, knowledge repository,
locations and flow flexibility are also covered in the literature. The
work process models to be created during the modeling sessions must have
sufficient entity types to provide the information relevant for
reaching the research goal. In this research, the workflow model is
serving as a base for deriving the network relations. Therefore, the
composition elements that will be chosen are: the activities and order,
the information flow (input and output) and the actors. The tools,
resources and the time factors will not be considered. This will lead to
a theoretical workflow model, based on the desired information flow.
The second part of the research, phase 2, is to check
the real network existing in the taskforce by carrying out a Social
Network Analysis (SNA): identifying how the information is really
flowing. The Social Network Analysis will be designed based on Cross
& Parker's network theory [29].
To visualize the results Node XL has been used. The data will be
quantitatively examined on individual level from the aspects of degree
centrality, betweenness centrality and eigenvector centrality [30].
These aspects are defined as follows. Degree centrality is a simple
count of the total number of connections linked to a vertex. Betweenness
centrality is an indicator of a node's centrality in a network. It is
equal to the number of shortest paths from all vertices to all others
that pass through that node. A person with few connections could have a
high eigenvector centrality if those few connections were themselves
very well connected.
There are several data collecting methods for social
network analysis. Ideally, network approaches tend to study the whole
population by means of census, rather than by sample [31].
Therefore, at one side of the spectrum of approaches is the "full
network" method, which requires collecting information from all actors.
This approach yields the maximum of information, but can also be costly
in terms of time and effort. Since there is no definite limit to the
number of people who are interrelated, full network is in any case not
practically possible. In this research, the snowball method is selected [31],
since the research has a relatively limited target group: the project
team. Therefore, the ties among people in the company but not working on
this project will not be studied. The snowball sampling approach which
is modified for use in this network analysis is as follows: the first
round initial participants are all project members in Amsterdam office,
including team members from different engineering disciplines, support
and administration staff, management team as well as the owner
representatives. The subjects are encouraged to name their colleagues in
New Delhi and in the USA office. Responses from the above-mentioned key
actors are further used to select a second round of participants,
limited to those who have been identified by two or more first- round
participants. The "two or more" technique is adopted from a network
study from Smythe, et al. [32].
There are many types of relations that can be studied
in network research. For instance, people can be asked to name the
person who helps them solve problems or the person who helps career
development. Therefore, different questions can reflect different
aspects of how people are connected to each other. In the book The
Hidden Power of Social Networks by Cross and Parker [29]
a thorough framework covering different aspects of surveying social
networks is presented that provides good foundation for this research.
Considering that the aim of this research is to improve the work-related
collaboration for a particular project, the survey design should focus
on the work process of the project taskforce. Moreover, the aspects to
be examined should be consistent with the aspects derived from the
workflow procedure study. According to the conclusions from the previous
paragraph and combining them with organizational chart information, the
collaborative aspects used in the current study are presented inTable 1.

Apart from the work-related interactions mentioned in Table 1,
which are the visible aspects of relationships, previous social network
research discovered that social network analysis could also seek to
reflect the invisible motor and knowledge sharing behind the interaction
process. The elements that should be considered in this respect are
knowledge awareness (who has the skill and or expertise) [27,33], accessibility (the willingness to share that knowledge) [27,34-36] and trust (your confidence in the knowledge that you received) [37].
In phase 3 the results of the workflow model will be
compared with the outcomes of the social network analysis and this will
lead to recommended improvements to the organizational effectiveness in
phase 4.
The research methodology and the various steps
followed as described in the previous in the previous paragraph is
schematically shown in Figure 1.
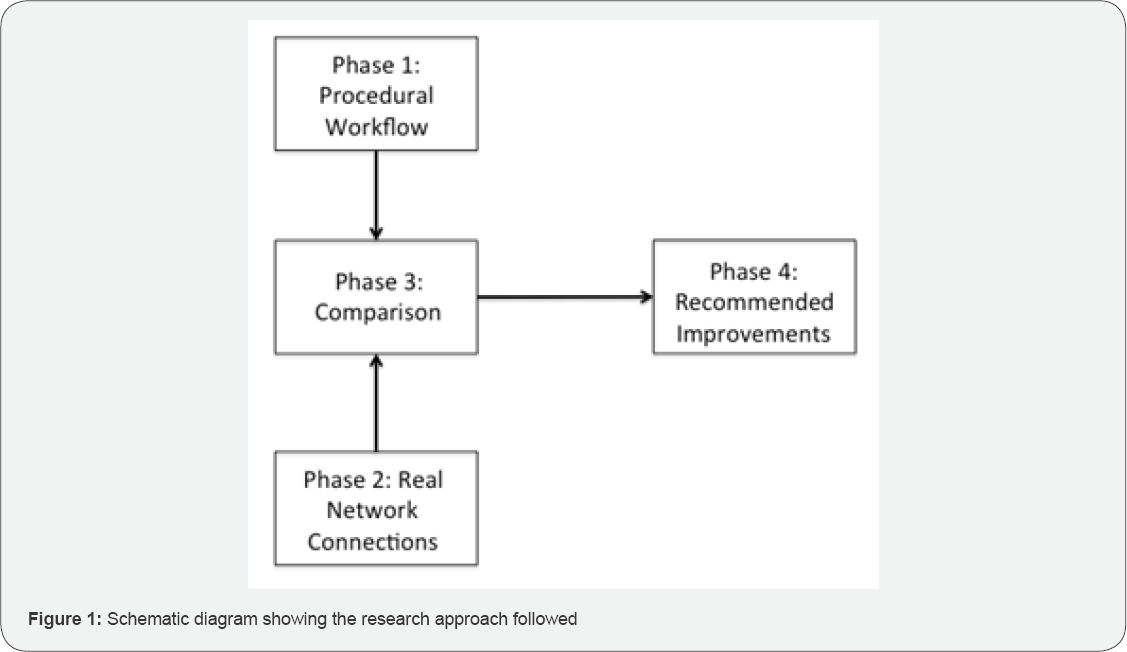
FEED Business Process Model
Workflow model
The FEED phase entails the work required to produce
process and engineering documentation in sufficient quality and depth so
as to adequately define the project requirements for detailed
engineering, procurement and construction and to support a rough project
cost estimate. The FEED package could be used as the basis for bidding
the execution phase contracts and is used as the design basis. A good
FEED should reflect all the owner's project specific requirements and
avoid significant changes during the execution phase. For large sized
projects, FEED contracts usually take around one year to complete.
During the FEED phase, close communication between owner, operators and
engineering contractor is needed to work out the project specific
requirements [38].
Owner’s time saving strategy resulted in contractor being both the FEED
and the EPC contractor. Since Contractor will also carry out the EPC,
there is no bidding procedure in between. The FEED package will mainly
be used as the design basis for detailed engineering design and
estimation for the investment.
Deliverables are the output from one stage and the
input to the next stage. Deliverables are always the communication media
and the checking points between disciplines, owner and contractor in
engineering work processes. FEED deliverables are often handled not as
single instances but in the form of documents, which act as carriers for
the design data and will be reviewed, approved and transferred to the
EPC phase. These documents differ widely in form and content, ranging
from word documents, reports, job bulletins, datasheets and calculations
to documents containing graphical data or even digital models.
Based on both contractor's standards and owner’s
requirements, a list of main FEED deliverables for this particular
project has been defined. In the business process model for the FEED
only the deliverables, which are necessary for the end product/project
design have been taken into account. Other project deliverables (such as
Project Execution Plan, Refinery Reconfiguration Plan and Project
Master Schedule) will not be investigated. After choosing the main FEED
deliverables and taking the dynamics of documentation into
consideration, the next step is to model the workflow based on the
standard project execution procedure. The method that is used to gather
the model input information is a company document study. The Project
Activity Model (PAM) with associated Activity Plans, Project Requirement
Checklist (PRC), Project Work Breakdown Structure (WBS) and other
practices for each discipline are examined in order to derive at the
activity sequences and identify the actors involved.
All these three main documents: PAM, WBS and PRC
provide holistic information to understand the FEED activity and its
actors. However, none of them show the sequential relation visually. PRC
is a checklist and mainly focusing on describing a clear scope for a
particular project. WBS divides the FEED package into manageable tasks
but only has the links of activity in vertical/hierarchical level. PAM
contains the information for the sequence and dependency of the tasks,
but not presenting them in a graphical manner since the activities are
not linked via
lines. Besides, the whole PAM system is too complex,
includes all the activities and is not project specific. For study
purposes, a simplified workflow will be derived based on PAM, PRC and
WBS, and focusing on the FEED deliverables.
The whole workflow of the major FEED deliverables is shown in Figure 2
with each block representing a deliverable or a task with on the top
the responsible discipline. There are three types of dependencies shown
in the model. One-way arrows represent the sequential dependency.
Two-way arrows in orange show the mutual dependency, which means that
there is an iterative and interactive process when developing both
deliverables. The third type of dependency is the circular dependency
shown, for example, between the P&IDs and the HAZOP study. The HAZOP
study is performed based on P&ID while also going back to P&ID
development. The design specifications from the owner are the starting
point of the whole model. The contractor promotes optimum interaction
between the owner and the contractor team on a daily basis. The premise
is that close contact and coordination between discipline leads from the
owner and the contractor will facilitate and enhance the project
execution. More specifically, in the team formation and organizational
structure, the contractor team is set up in order to mirror owner’s
organization to streamline the communication channels between
counter-parts.

All the roles and responsibilities are aligned with
contractor's standard execution model for the FEED stage. Engineering
disciplines such as mechanical, piping and civil report to the
engineering manager, while process is a separate discipline and reports
to its own process manager.
Multi-locations
There are four offices involved in the FEED phase.
The Amsterdam office is the leading design office of the contractor
Owner representatives are located together with contractor staff in the
Amsterdam office and formed up teams of counterparts in order to improve
the team integration. The Amsterdam office has connections to the other
three offices. The USA office is the main design & engineering
office of the owner during the FEED phase. The decision makers and
gatekeepers of this project are in this office and they pay close
attention to the schedule and cost. This office assigns design engineers
as representatives to the Amsterdam office. Therefore, at discipline
level, the management team, project control team, process and
engineering disciplines from the USA office have contacts with Amsterdam
as well as the refinery site. Also representatives from the refinery
operations department were present in the Amsterdam office. At the
refinery site office, the owner's operations and maintenance team is
located. This team mainly consists of process engineers, equipment
engineers, electrical engineers and business supporting staff. As a
European subsidiary, this office has contacts with the main office in
the USA. At the start of this study, the Site Based Engineering Team
(SBET) is just formed and is located directly at the site office.
Refinery site office has contact with both Amsterdam office and the USA
office, especially for the activities related to the revamp task. The
New Delhi shares the work with Amsterdam office in almost all the
engineering disciplines, especially the disciplines involved for
developing 3D model (piping, electrical and civil). Because the revamp
part of work is not shared with New Delhi, this office has no direct
contact with the refinery site office or the owner in the USA office.
Using the organization charts of both the owner’s and contractor's team
together with the business process model, all relations have been
tracked down and summarized in Table 2.
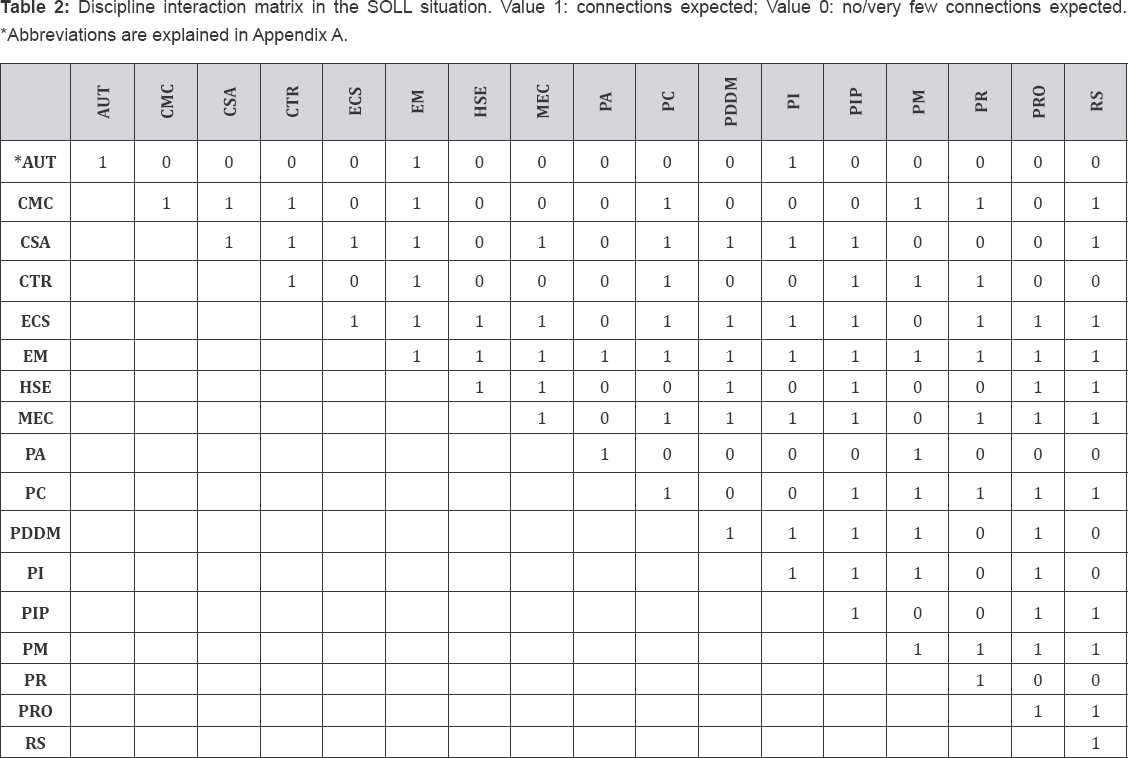
Based on the workflow and the organizational
arrangement, it can be expected that most frequent contacts should
happen in process and project control. People from these disciplines are
expected to adapt to the owner company culture quickly and be able to
interpret and transfer the information accurately and efficiently to
other disciplines. From the workflow chart in Figure 2,
process discipline is the first one to take the initiative for the FEED
activities. This discipline has to fulfill the specific role to
translate the job requirements into specific scoping deliverables for
the other engineering and supporting disciplines. A close cooperation
between the process discipline and the owner organization is therefore
inevitable. Considering the fact that the contract type is reimbursable,
the owner pays close attention to the cost, schedule and change orders
via project control discipline. Therefore, there are many owner
representatives from project control located directly in Amsterdam
office together with contractor team and they have frequent and
extensive communication with each other. Besides, these owner
representatives need to keep the senior managers from the US office well
informed of the progress. Therefore, this discipline also will have
more contact with US office.
Three levels of interaction
The first outcome is a workflow model in Figure 2
that depicts the main work related activities, their sequence and
interdependencies as well as the responsible disciplines. The results of
the network information in this chapter are clustered on three levels:
Discipline coordination level: Visually, the
workflow model shows that the process discipline is the initial
discipline, which has to translate the design specifications to scope of
work for other disciplines. At the same time, it takes over the design
& engineering work from the owner and keeps on developing the PFDs
and P&IDs. These are the basic deliverables for the FEED. Therefore,
process discipline is the key player in the project. Other engineering
disciplines follow directly after process and provide input for the
supporting disciplines like project control, procurement and
contracting.
Office work sharing level: Amsterdam office is
expected to connect with all other three offices. New Delhi office
mainly connects to Amsterdam office. USA office, Refinery Site office
and Amsterdam office are expected to be connected to each other.
Owner team integration level: The organization
structures, team compositions from both owner and contractor are
investigated as well as the counterpart relations. Close contact is
expected to be in the process and project control discipline.
All the network relations derived represent the SOLL
(=as it should be) situation. These are not the optimized but the
expected relationships for the project taskforce. In the following
paragraphs carrying out a social network analysis will discover the real
network relations (=IST).
The Real Social Network
In order to investigate the actual relationships a
Social Network Analysis has been executed for which a survey has been
designed. In a social network survey, the responses can be gathered in
several ways. Ticking the names from a list of the persons the
respondents have relations with, giving a score or ranking, or giving a
value assessment of their perceived contact level with each person. By
far the most common approach to scale (assigning numbers to) relations
is to simply distinguish between relations being absent (coded 0), and
ties being present (coded 1). The result of this measurement is shown in
0/1 mode and therefore is called binary scale measurement [29]. The binary measurement method has been chosen for this survey because of its simplicity.
Kossinets [39]
assessed the impact on the structural properties of social networks of
three kinds of missing data: network boundary specification
(non-inclusion of actors or affiliations), survey non-response, and
fixed choice design (a list of names is given already). He concluded
that setting the network boundary too narrow and giving a fixed list of
names to choose from can influence the network structure greatly since
some names will not be mentioned, potentially resulting in stochastic
omission of some fraction of actors from the network. As explained, the
targeted survey subjects are all members of the project team, wherever
their location. Open questions were formulated, asking the respondents
to nominate people instead of choosing from a predefined list. The
non-response effect is generally relatively small in network analysis.
When the survey asks actors to name peers with whom they interact, the
nonresponse effect can be balanced out by reciprocal nominations [40].
The social network survey is launched by using the
snowball method with the first round carried out in the Amsterdam office
to 110 people. 80 of them responded. Hence the first round response
rate is 73%. The second round is launched to 23 people, located in the
USA, New Delhi and Refinery Site office. 7 of them responded. This
accounts for 30% of the targeted second round group. The total number of
participants is 87. Through these participants, 163 people are
discovered and mapped in the network. The respondents as well as the
entire network discovered are characterized as a diverse population
representing a range of discipline expertise from both owner and
contractor. Most of the engineering disciplines participated well in the
survey. Some management and supporting disciplines have actively
participated. The owner and contractor participation distribution is
consistent with the spread in the organization: the owner accounts for
39% and contractor accounts for 61% of respondents. Therefore, the
participants sufficiently represent the whole team.
For confidentiality reasons, code numbers have
replaced the names of the participants. Each code number starts with the
discipline abbreviation followed by a number. The entire social network
for the project is depicted in Figure 3,
with nodes (vertices) representing actors and ties (edges) representing
connections between them. Each circle represents a discipline. The
actors are connected within each circle and also with actors from other
circles. The most connected discipline is automatically placed in the
centre. The social network analysis result is mapped by using no arrow
(undirected) ties. It is the overview covering all the relationship
types: information input-output, problem solving, decision-making and
recognition in line with Table 1.
There are in total 163 people (vertices) discovered in the whole
network and 769 relationships (edges) are mentioned of which 224 are
two-way confirmed answers (duplicate edges) and 545 are one-way mentions
(unique edges). After merging the duplicate edges, the total number of
connections discovered is 657.
From the overview map in Figure 3,
it is difficult to see that all disciplines are connected to each
other, what can be seen is that the process and other engineering
activities are well connected. No isolated islands exist at the
disciplinary level. Process discipline is in the centre and taking the
leading role fulfilling FEED design work. On the individual level, this
general overview also reflects that no single individual is isolated.

However, it can be found that some disciplines
include more outliers than others. In the civil structure circle and
mechanical circle, there are several people being mapped by only holding
one connection to the rest of the group. When tracking back to the
function of these outliers, it can be found that they are most often
subject matter specialists who work in more projects at the same time
and are not physically located with the project team. They serve more in
an advisory capacity than being responsible for the task. In other
cases, for engineering management, process, piping and project control
disciplines, each individual is more actively connected. No significant
spread is seen in the number of connections of individual members of one
group. Each circle on the overview map can be regarded as a sub-graph
and can be separately studied. That will show the connections within one
single discipline. It is assumed that people who work on similar tasks
have more interactions than those who work on different topics.
Process discipline is highly intra-connected with
each person having on average connections with 3 people in the same
discipline. Among other engineering disciplines, piping is most
connected with each person being connected to approximately 2 people in
the same discipline. Mechanical and piping have a similar size of group
(19 and 17 people, respectively) but the mechanical discipline is less
intra-connected even with two more people. The same can be seen when
comparing the electrical control department with civil structure, where
civil is clearly less connected. This result is very logical for
mechanical, considering their specialty on different kinds of equipment
(from heat exchanger to furnace, from reactor to compressor). They are
very much focused on their own area of work and are educated in
specialized areas. While, in process or piping, people usually have the
same kind of knowledge. It is easier and more necessary for them to
transfer and exchange knowledge with their discipline. The project
control and engineering management disciplines also have high
intra-connecting scores, around 3 people/person, which means that these
two disciplines are very well integrated as a group.
The connections among different disciplines can be shown graphically (Figure 4), a graph that is less cluttered, but it is probably more clearly shown in a quantitative way in a matrix. The matrix in Table 3
shows how many connections are mentioned by the respondents clustered
by discipline. It also includes the internal connection within one
discipline in the diagonal line. The larger the number of connections
is, the stronger the link and more frequent the communication between
the disciplines.
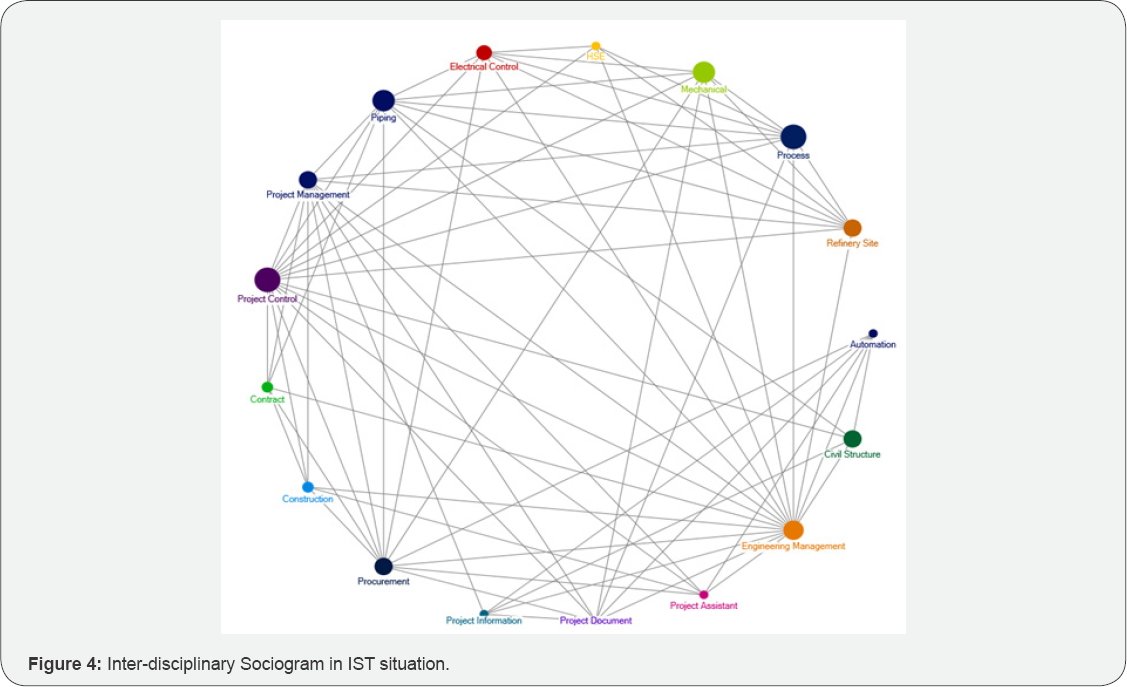
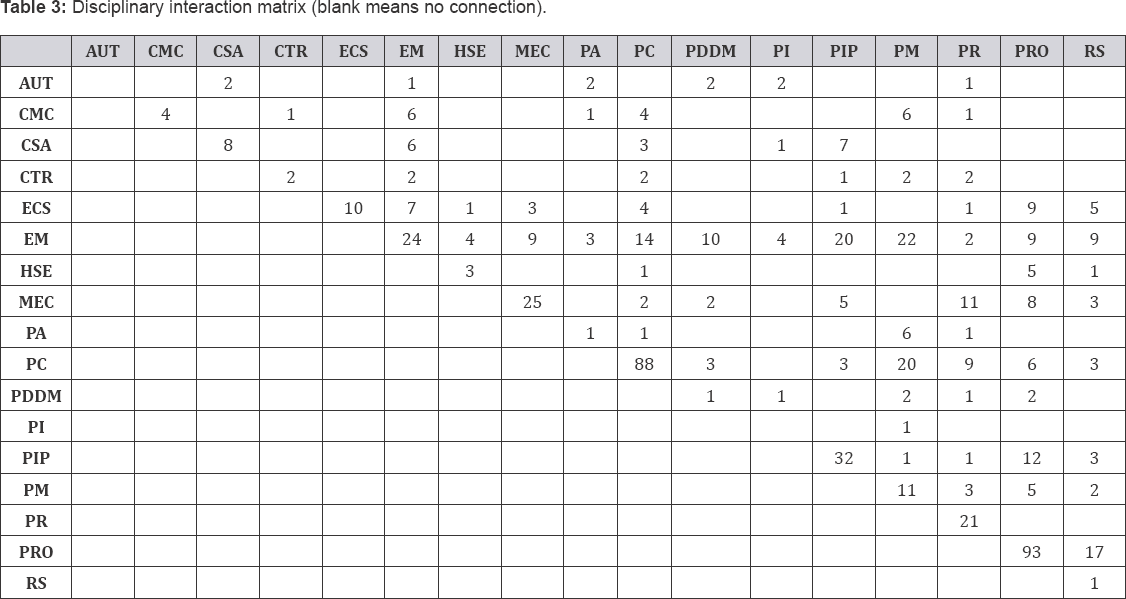
As can be seen there are many empty cells which might
represent missing connections. However, to accurately analyze this
matrix, the no-connection judgment should not be made directly based on
the visualized results. It is not always necessary, nor desirable, to
connect all the disciplines together. Only when it is necessary
according to the
Work-related procedure, should two disciplines have
connections. Too many connections will bring an overload of information
and thus decrease the productivity. Therefore, this matrix provides a
very good overview of the IST situation, which can now be compared with Table 2
representing the SOLL situation derived from the workflow study to find
the structural gaps and missing links. This comparison is provided in Table 4.
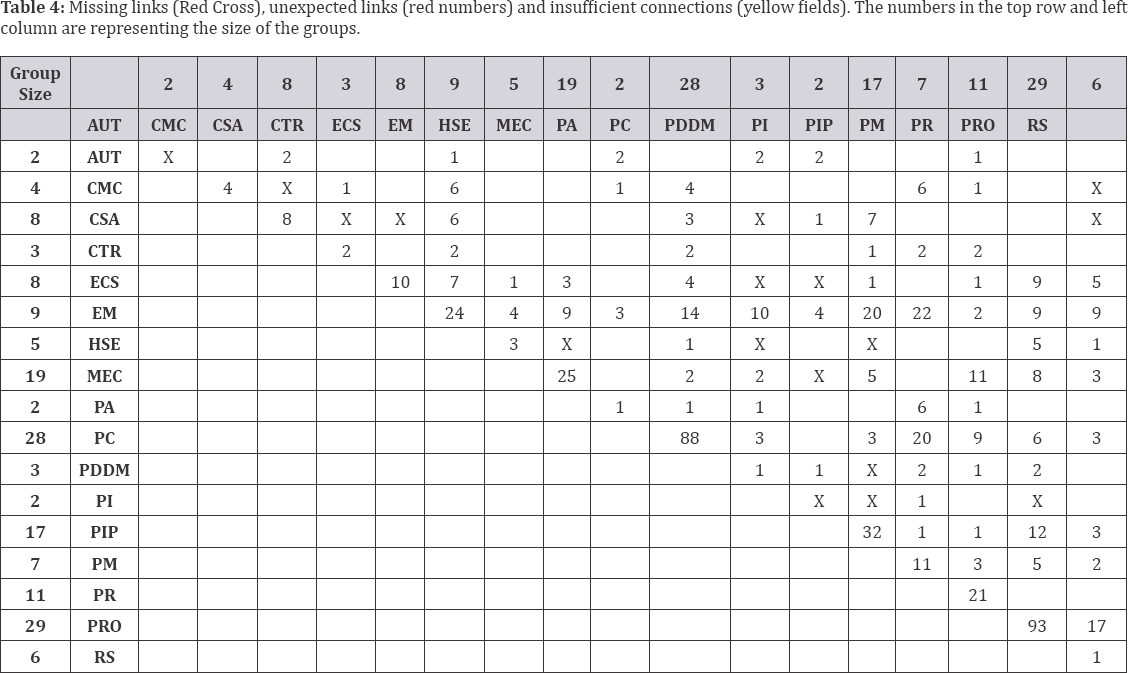
When only the links between owner and contractor are
studied, it is again clear that the process discipline is very well
connected both internally with owner staff within the process circle and
externally with owner staff from other disciplines. Similarly,
contractor's engineering management, electrical control system,
mechanical and project control disciplines are very well integrated with
the owner team. From this analysis can be seen that the piping
department has no internal connections: piping staff are mostly
connected with the owner staff from mechanical, process, engineering
management and refinery site. Given the fact that the project team will
roll over to EPC phase when piping discipline plays a more central role,
the owner- contractor integration in this particular discipline should
be an area of attention.
Apart from mapping the connections nominated by the
taskforce, respondents were also asked for missing links. As a response
the owner process engineers indicated that they wished to have more
direct contact with contractor staff in the New Delhi office. On
discipline level, a very distinguishing result is that many disciplines
stressed to have more interactions with the refinery site. Second
finding is that project engineers proposed to have more connections with
HSE. Project control staff indicated that they would like to get more
help from the engineering disciplines to help understand scope of work
and work sequence.
The quantitative analysis aims at identifying
individual network influences on the whole project team. There are four
parameters that will be measured in the study [30]:
· Degree centrality: directly contact numbers
· Betweenness centrality: bridge scores between people
· Closeness centrality: distance scores for broadly connected people
· Eigenvector centrality: influence scores for strategically connected people
Except for the degree centrality, for which the
absolute value directly indicates the number of connections; other
centralities are better to be interpreted using the ranking and relative
value instead of the absolute value. Figure 5
shows degree centrality on the x-axis, betweenness centrality on the
y-axis and the node size represents the closeness centrality. Since the
quantitative method is mainly suitable for individual network influence
study, this research also focuses on evaluating and discovering the
most centralized staff. Besides, considering the role and function of
each individual, special focus is given to the lead engineers and the
management team members, who are coloured green (=contractor leads) and
blue (=owner leads). The red nodes are common staff.

Two lines, representing the averages, split the whole
graph into four quadrants. The people who are shown in the first
quadrant have relatively high betweenness centrality and degree (above
the average level). It can be noticed that most of the discipline leads
from contractor and owner belong to this category. Logically, there is
almost no one in the fourth quadrant (Q4) since without possessing a
number of direct contacts it is not easy to be acting as a bridge
between people. The left bottom quadrant (Q3) contains the outliers of
the network; this group actually contains quite an amount of people.
However, in the graph, the nodes with same value are covered by each
other. People in the right bottom quadrant (Q2) are active networkers
because they have above average direct contacts. Supporting and
management actors (EM, PM and PC) are in this category and are actively
engaged networkers indicating that they facilitate the process, but
without them, the real engineering work can still be achieved.
The degree of centrality (vertex) is a count of the
number of unique edges that are connected to it. The higher the numbers
of ties an actor has, the more influential he or she may be. The average
degree centrality of studied participants is 8. By checking the x-axis
on Figure 5,
EM03 has the highest degree centrality score: 29 direct connections.
PROO6 and EM04 have the same degree centrality: 25. EM03 is the
engineering manager from contractor side.PRO06 is a lead process design
engineer from the owner and EM04 is a project engineer from the owner.
EM03 and PRO06 also largely exceed the second level of high betweenness
centrality: PRO13, EM04, EM09, PC13. This indicates that these two
actors really develop their function role as much as possible as manager
and lead engineer and they have high potential of interpersonal skills.
This can also indicate that the network is highly dependent on these
two central actors. Any job changes happening to these key actors may
influence the connectivity for the project team at least for a short
period.
Betweenness centrality is a measure of how often a
given vertex lies on the shortest path between two other vertices. More
generally, vertices that are included in many of the shortest paths
between other vertices (called geodesic distances) have a higher
betweenness centrality than those that are not included on such paths. A
node with high betweenness centrality has a large influence on the
transfer of items through the network, under the assumption that item
transfer follows the shortest paths. This can be thought of as a kind of
"bridge" score, a measure of how much the removal of a person would
disrupt the connections between other people in the network. The idea of
brokering is often captured in the measure of betweenness centrality.
Therefore, networks that have individuals with high betweenness are
vulnerable to having information flows disrupted by power plays or key
individuals leaving.
Closeness centrality is a measure indicating the
social distance. The higher this value is, the more influential a person
is considering the distance he/she needs to get connected to others.
One property of closeness centrality is that individuals who are highly
connected to others within their own cluster tend to have a high
closeness centrality [41].
For this centrality value, many people are having the same highest
score value. Among them, the engineering discipline leads from
mechanical, piping, civil are found as well as the process leads. This
result indicates the lead engineers fulfill their network functions very
well in their own disciplines. High centrality/connectiveness might be
an indicator for overload of an individual.
Eigenvector centrality is a more sophisticated view
of centrality: a person with few connections could have a very high
eigenvector centrality if those few connections were themselves very
well connected. Eigenvector centrality allows for connections to have a
variable value, so that connecting to some vertices has more benefit
than connecting to others. Similar to degree, eigenvector centrality
extends itself to calculate how "connected" are the nodes connected to
you. Therefore, usually highly connected individuals within highly
interconnected clusters have high eigenvector centrality [41]. In the social network analysis result (Figure 3)
engineering management, project management, process and project control
group are very well connected within their own group, and at the same
time, very well connected to almost all the other disciplines.
Therefore, the calculation result of the highest individual score of
eigenvector centrality mostly comes from these three disciplines.
Practical Results
For practical applications the results from the
business process model (SOLL) are compared with the outcomes of the
social network survey (IST). The comparison is carried out in two steps:
i. By checking the binary numbers in both situations, the missing links and/or unexpected links can be found and
ii. By checking for existing connections whether the
amount is consistent compared to the group size and focusing again on
the three levels: discipline, office sharing and contractor-owner
integration [42].
On the discipline collaboration level, missing links
appear mainly in civil discipline and HSE discipline. Civil is very well
connected to piping and project engineers. It is suggested to pay more
attention to the work coordination with mechanical and electrical
control discipline. In addition, the connection among civil,
construction and refinery site needs to be strengthened. Considering the
size of the discipline, some connections are mentioned but are
identified as not sufficient. Piping and electrical control are expected
to have more direct contact with each other instead of through process.
From the owner side, there is interaction between procurement and
construction, but this link is missing in the contractor team. There are
only five connections between process and HSE. It is suggested to
promote a way to bring HSE knowledge more to the process design.
On the office collaboration level, even though the
four offices are connected as expected in the SOLL situation, the New
Delhi office is largely neglected except for the piping discipline. The
detailed number of connections reveals more information and it can be
seen that even though most of the technical disciplines are mentioned
from the New Delhi office, they are usually only mentioned once and only
the lead engineer is mentioned. In contrast to other disciplines,
piping staff have strikingly more connections with New Delhi. Through
observation, it can be found out that the piping lead in Amsterdam
office set a very good example by daily communicating with the New Delhi
office colleagues. This lead really pays attention to the work sharing
and has more personal care for his co-workers in the other offices. It
is suggested to take the piping lead as a leading example for other
disciplines and pay more attention to and share work with the execution
office in New Delhi.
On the owner-contractor team integration level, the
process, project control and engineering management team are very well
connected to the owner. The piping discipline, even without obvious
counterpart, finds its own way to forward their problems and carry out
discussion with the owner, mainly through mechanical/project engineers.
The interaction at the refinery site is still weak because of the recent
set-up of the onsite team [43].
The development of a business process model for a
particular project phase in combination with SNA has the potential to
improve the effectiveness of integrated project teams. Via the study and
the combination of the two methods a number of shortcomings in the
project team organization have surfaced. Due to the combination of the
models the real time differences compared to the (theoretical)
organizational model have helped to further strengthen the team,
incorporated people more closely to the team and identified areas that
needed more intensive collaboration in order for the integrated team to
be as effective as possible. As mentioned in the introduction, this has
not been a once-off exercise. The involvement of subsequent students in
the project team put the focus on the EPC phase and subsequently also on
the collaboration between the main contractor and their sub-contractors
and suppliers [44,45].
Conclusion
This research innovated the methodology to study a
complex project by combining the social network analysis with business
workflow modeling forming a SOLL-IST comparison framework. Firstly, this
research can be seen as an extension of the business process management
methodology. It started by adopting the workflow concept for the
process industry. Furthermore, the research focused on the "people"
aspect in the workflow and build upon the idea of discovering social
networks from the workflow.
The social network analysis was adopted and
tailor-made survey questions were developed. In traditional social
network analysis, it is difficult to interpret the result, especially,
to tell whether a missing link really exists. More background
information has to be given in order to judge if a connection is
necessary depending on what kind of relations are being studied. That is
why in this research the workflow study provides a better base for
analyzing and interpreting the social network result.
In addition, this research provided insights into the
collaboration in the process industry by targeting the three levels of
collaboration that exist in many projects in this industry. It combined
the different collaboration themes from the literature study:
disciplinary collaboration, globally distributed project team
collaboration and client-contractor team integration. This study
provides a more holistic view and the findings from this research also
showed that these three levels of interaction are very much intertwined
and are influencing each other.
The project team has acted on the findings by looking
at alleviating the overload on some key players that surfaced during
the analysis of Figure 5,
and stimulating relationships that have been weak or non-existent. By
doing that the coherence between the various locations and disciplines
is further improved and the work processes become even more robust and
effective. The client and contractor made the deliberate choice,
however, that full team integration is not a goal of the project. Too
much integration between disciplines could disturb the production
machine and construction effectiveness. The research will be continued,
however in the EPC phase to further integrate the two teams aimed at
successful project completion and subsequently also on the collaboration
between the main contractor and their sub-contractors and suppliers.
For the multi-actor study, only owner and contractor
have been considered. However, it is suggested to involve the
subcontractors and suppliers in the subsequent study during the EPC
phase. Another interesting element for future study would be the
influence of contract type. The reimbursable nature of the project may
lead to more owner staff in the project control discipline in order to
keep detailed track of the project cost and schedule.
The overall conclusion is that the development of a
business process model for a particular project phase in combination
with SNA has the potential to improve the effectiveness of integrated
project teams.
For More Open Access Journals Please Click on: Juniper Publishers
Fore More Articles Please Visit: Civil Engineering Research Journal
Fore More Articles Please Visit: Civil Engineering Research Journal
Comments
Post a Comment